As far as Corey Williams is concerned, we’re walking on “hallowed ground.”
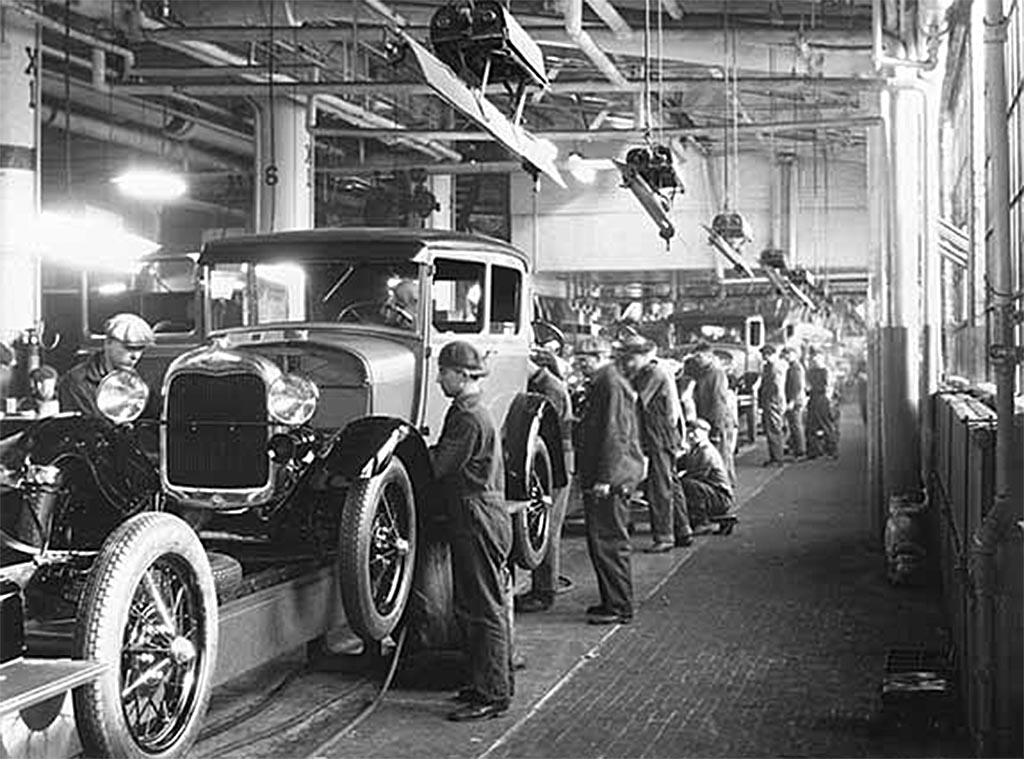
A year ago, there was nothing but a dusty parking lot where Ford Motor Co.’s new Electric Vehicle Center now stands. But dig deeper into the past and you realize this was the site of the original Ford Rouge Assembly Plant where generations of blue-collar workers built everything from Model A sedans to Mustangs to F-Series pickups — as well as armor, engines and tanks as part of the “Arsenal of Democracy” during World War II.
Starting next spring, this new factory will begin building the new Ford F-150 Lightning, the all-electric pickup truck has so far garnered over 150,000 advance reservations since it was unveiled in May. That’s part of a $30 billion electrification plan Detroit’s second-largest automaker has in play.
Rolling out the first battery-powered version of Ford’s iconic pickup — the nation’s top-selling truck for 44 years — might be significant enough on its own. But the new Electric Vehicle Center is also functioning as a research lab that could radically change the way cars and trucks are built all over the world.
“This is hallowed ground. This is history,” said Williams, the plant manager. “This is where we are going from the past to the future.”
Where’s the assembly line?

Take a tour of the center, which is slowly launching early prototype production, and you can’t help but notice something missing. The moving assembly line that was originally introduced by company founder Henry Ford 108 years ago is gone. The assembly line is a fixture at all but the lowest-volume plants building cars virtually by hand — and slowly, very slowly.
That’s not the case here. With the $250 million expansion Ford announced on Thursday, the Electric Vehicle Center will be capable of producing as many as 80,000 Lightnings annually. That’s not quite as fast as the plant next door where traditional, gas and diesel trucks or built, but quickly enough that this is a radical departure.
Instead of a fixed line, partially assembled pickups are loaded onto AGVs, or Automated Guided Vehicles. These are, essentially, robotic pallets that creep along the shop floor, guided by thin magnetic ribbons carved into the concrete. Sonar sensors help make sure they don’t collide with one another or with the hundreds of workers who’ll soon populate the plant.
It’s not the first time AGVs have shown up in factories. General Motors started using them in the 1980s, primarily to deliver parts to workstations along the line. This is the first time they’ve been put to use in such a high-volume operation completely abandoning Henry Ford’s movable assembly line.
Getting workers plugged in
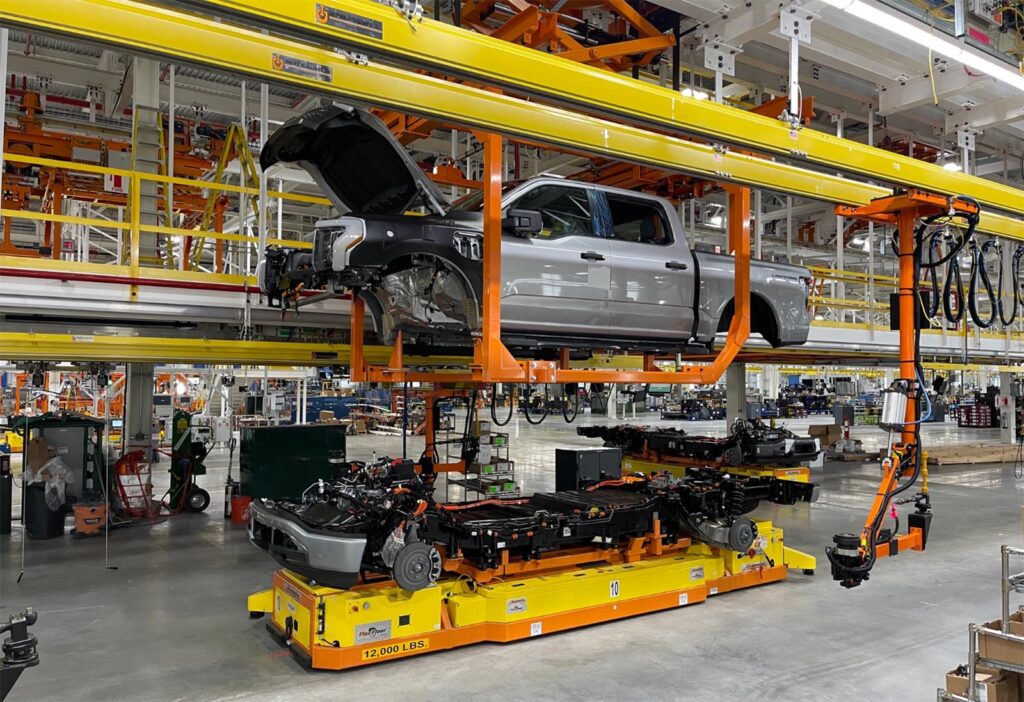
A major change, yes, but as far as Williams is concerned, one of the real hallmarks of the Center is the way workers become active, intelligent parts of the production process. Reaching their post, they log in at one of three tablet-style screens and can check on what happened during earlier shifts, then report in during their own.
Among other things, that will help Ford track and quickly resolve problems, explains Christopher Skaggs, who oversees Ford’s EV planning and implementation.
The AGVs not only move vehicles from workstation to workstation but they recognize the operators at each point, rising or lowering to maximize ergonomics, reducing stress and strains.
As is today’s norm, even in traditional assembly plants, there’s a high dependence on robots, including Transformer-sized beasts that can weld, glue and handle jobs like mounting windshields.
Robots and cobots
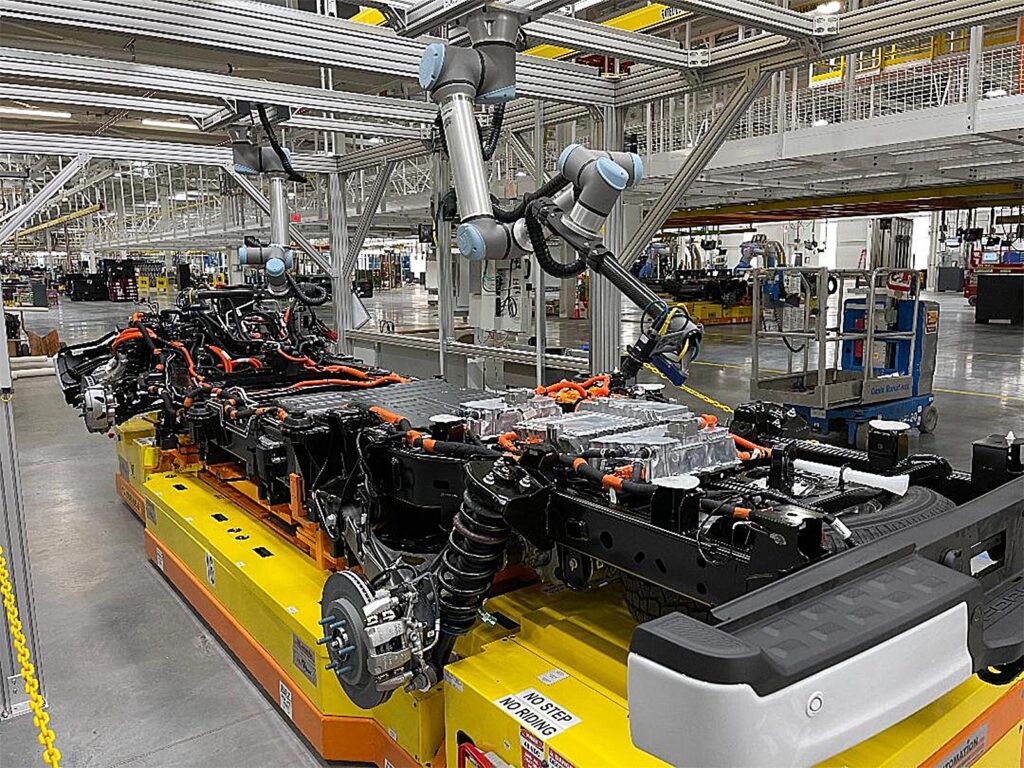
The center also introduces what Ford has dubbed “cobots,” or collaborative robots. Rather than being isolated and fenced off, they operate right alongside human workers. They can do tasks like sanding or, in this case, help their flesh-and-blood colleagues examine bodies for minor dings or damage using artificial vision.
The production process isn’t entirely unique. It still proceeds one workstation at a time and, as Lightning bodies follow their serpentine path they’re eventually snagged by an overhead conveyor, carried to the point where they are “married” to the chassis that contains each Lightning’s battery pack, motors and other drivetrain components, as well as wheels and suspension.
As the final assembly tasks are completed, the now operative electric pickups enter a series of inspection stations. One uses a massive robotic arm to press down on each Lightning’s cargo bed. Sensors built into the truck are designed to tell the driver how much weight it’s carrying. The test confirms that system is accurate to within a percent or so, explains manufacturing manager Liza Currie.
One last look
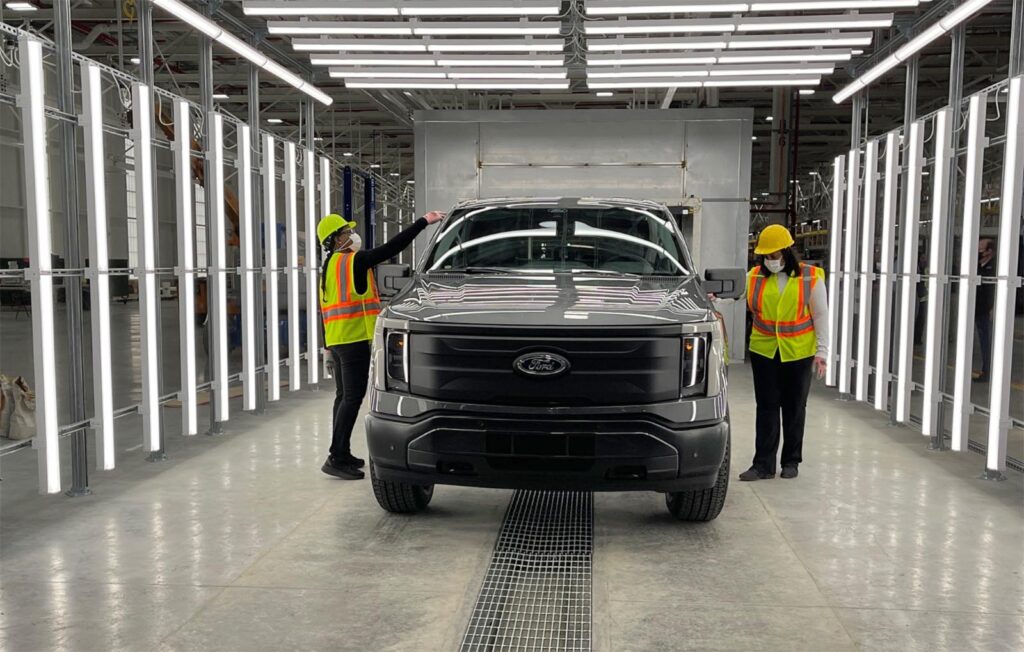
Finally, each truck will roll into a blindingly bright booth featuring dozens of carefully positioned lights. Human and robotic vision work together to ensure some exterior flaw — a ding, perhaps, or a chip in the paint — doesn’t get passed on to a consumer without being repaired.
As he surveys the new plant, Williams said he’s confident, “We’ve incorporated the latest and the greatest.”
Many of the new features will reappear in other Ford plants. But Williams hesitates when directly asked whether the conventional F-150 plant next door will switch to AGVs, abandoning it fixed line, when the truck goes through a makeover around 2025. That’s for higher-ups to decide, he defers, but it’s clear he sees the Electric Vehicle Center as the high profile test for a radical new system that could replace what Ford Motor Co.’s namesake gave to the manufacturing world a century ago.
“I believe what you’re seeing here,” Williams said, “is the beginning” of a massive transformation in the manufacturing process.